The Tribeca brick: Made from earth and water but (crucially) no fire

London’s largest life
sciences project is leading the way in sustainability by using low-carbon earth bricks for its first-phase basement walls—a move that could revolutionise carbon-conscious development. London’s largest life sciences project is leading the
way in sustainability by using low-carbon earth bricks for its first-phase basement walls—a move that could revolutionise carbon-conscious development.
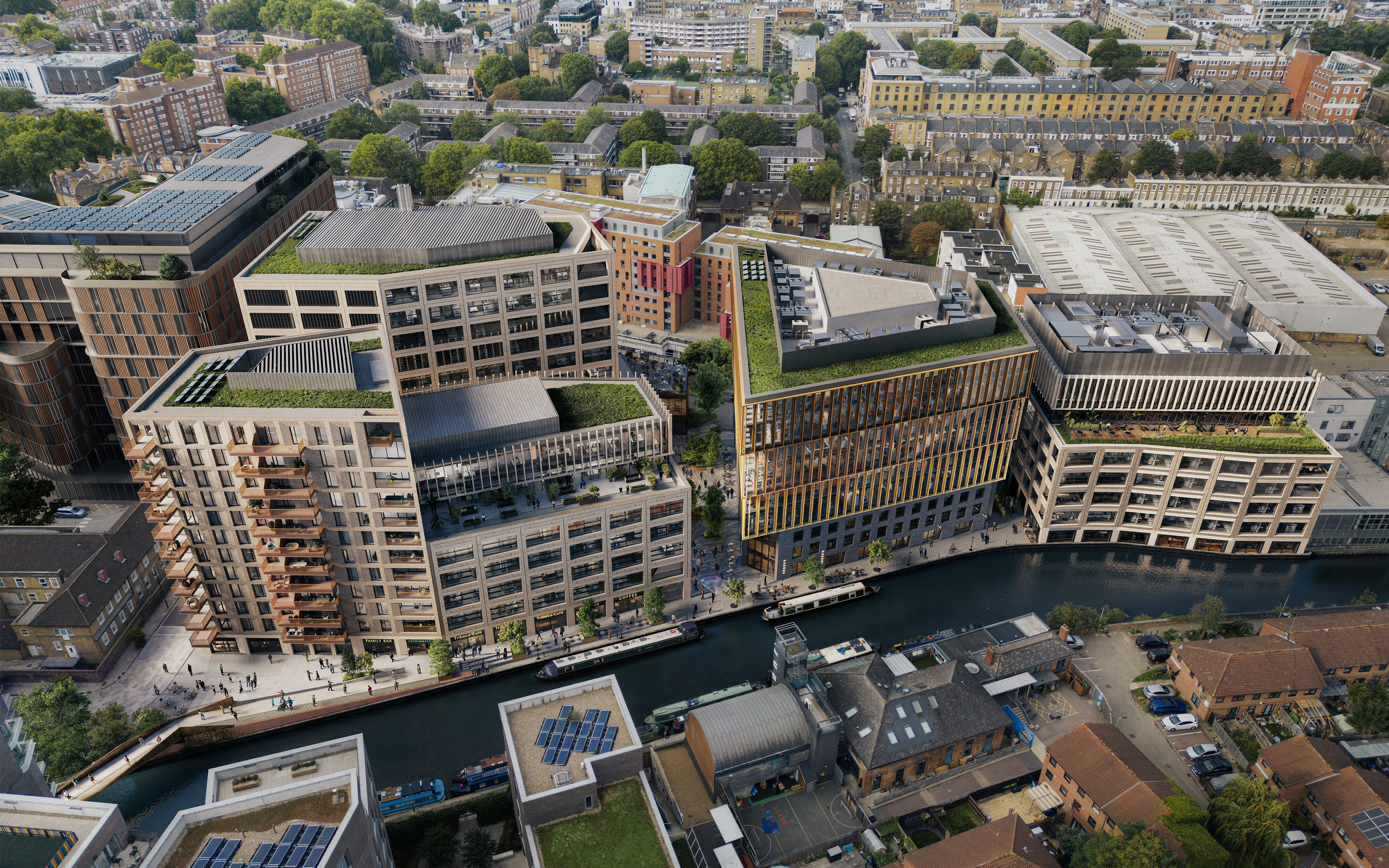
Demand for life sciences laboratory space in London
is surging. The Francis Crick Institute is converting its rooftop into labs, insurer LV’s former office is being repurposed for research, and British Land is adding lab space to its previously office-only Regent’s Place development. Amid this rising demand, the completion of the first phase of London’s largest purpose-built life sciences facility is a significant milestone. Initially conceived as an office scheme, Tribeca was reimagined in response to interest from the Francis Crick Institute, marking a major leap forward for the city’s bioscience sector. Demand for life sciences laboratory space in London
is surging. The Francis Crick Institute is converting its rooftop into labs, insurer LV’s former office is being repurposed for research, and British Land is adding lab space to its previously office-only Regent’s Place development. Amid this rising demand, the completion of the first phase of London’s largest purpose-built life sciences facility is a significant milestone. Initially conceived as an office scheme, Tribeca was reimagined in response to interest from the Francis Crick Institute, marking a major leap forward for the city’s bioscience sector.
Tribeca consists of four buildings, with the 112,340 ft² Apex being the first to complete. Apex is set to achieve BREEAM Excellent certification, while the goal for the remaining buildings is to reach Outstanding.
Serving as a test bed for the upcoming phases, Apex is pioneering sustainable construction methods, including the use of unfired earth bricks to minimize upfront carbon emissions.
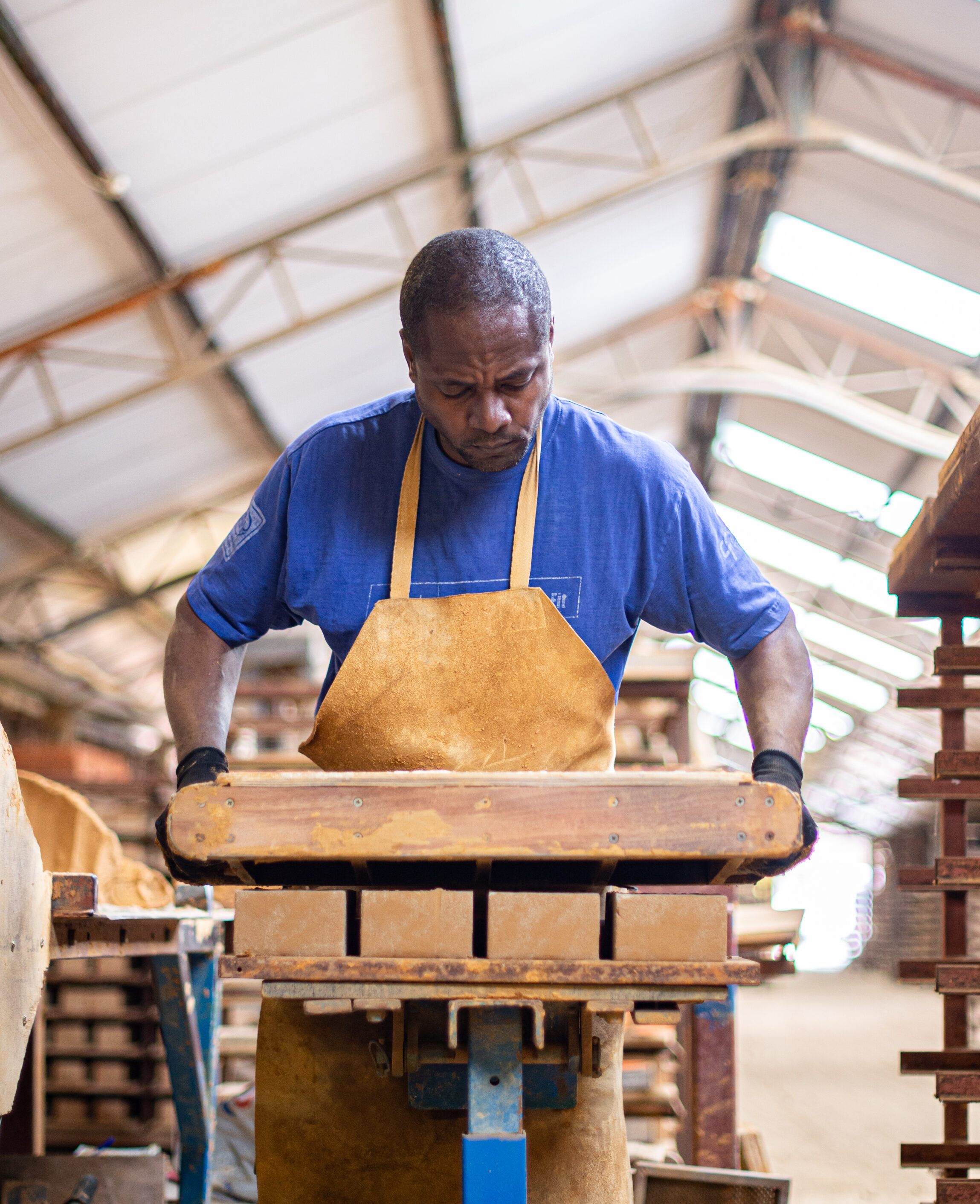
The brick has replaced
concrete blocks in the basement liner wall, which stands 5.9 meters high and includes insulation and waterproofing layers behind it. The key advantage is that producing earth bricks generates just one-tenth of the carbon emissions of concrete blocks. Additionally, unlike concrete, these bricks can be regenerated to create new ones. The brick has replaced concrete blocks
in the basement liner wall, which stands 5.9 meters high and includes insulation and waterproofing layers behind it. The key advantage is that producing earth bricks generates just one-tenth of the carbon emissions of concrete blocks. Additionally, unlike concrete, these bricks can be regenerated to create new ones.
“We must move away from building materials associated with resource depletion,” explains Nikolay Shahpazov, project architect at Bennetts Associates. He emphasises the need to transition from cemented or glued materials that cannot be reused to those that can be continuously reworked and repurposed.
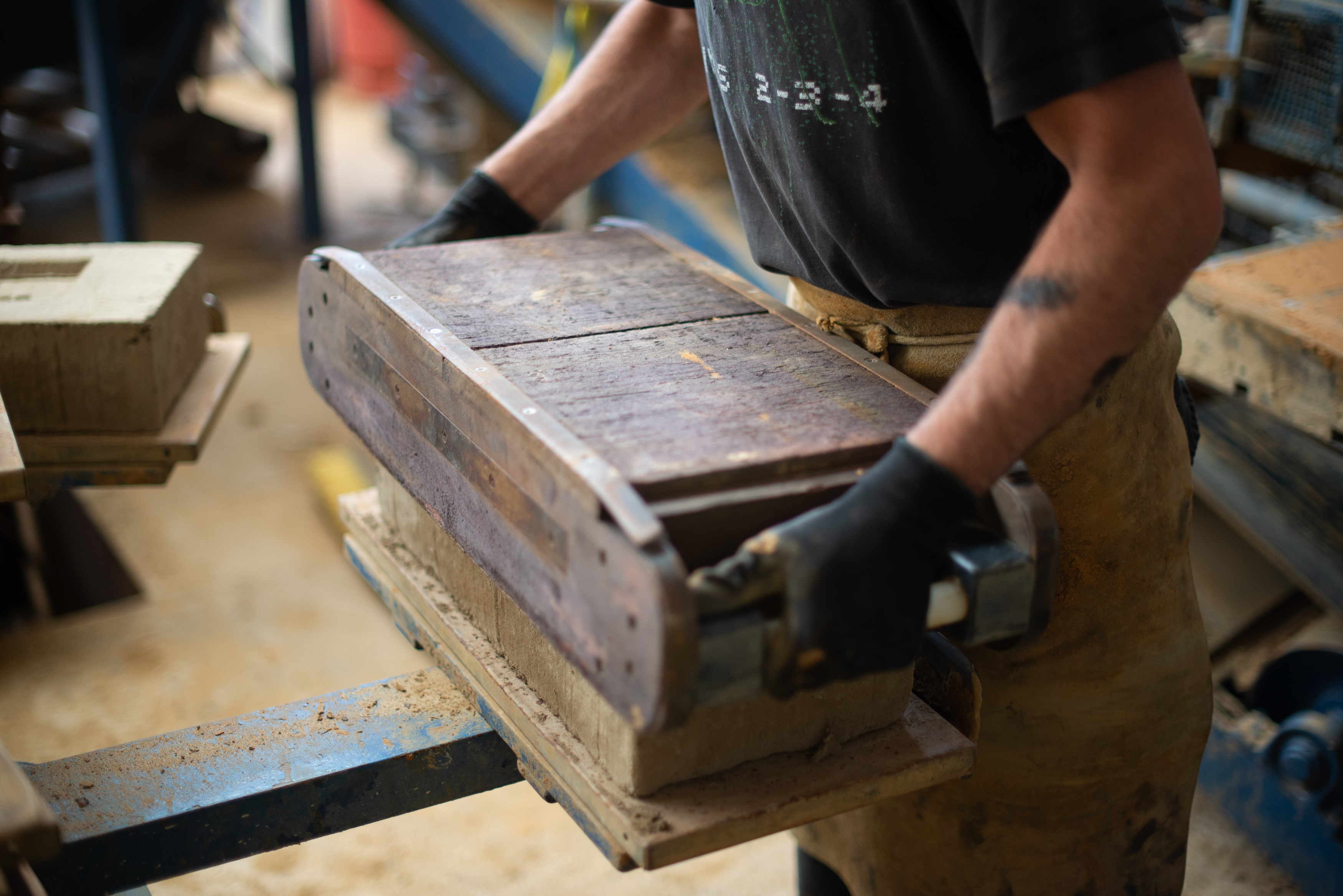
The project explored using excavated material from the site to produce the blocks, offering a dual advantage—reducing resource depletion while cutting landfill waste and associated taxes.
To achieve this, the team collaborated with HG Matthews, a Buckinghamshire brickmaker known for pioneering low-carbon brick production. While the clay subsoil at Tribeca contained more silt than typically used for brickmaking, it was still suitable for crafting earth bricks.
HG Matthews tested three different mixes: one with 100% Tribeca clay, another with 25% sand, and a third with a 50:50 clay-to-sand ratio. Each mix also included straw and water to create a workable consistency for molding.
Once shaped, the bricks were placed in an insulated drying room heated to 50°C by a woodchip boiler. After four to five days, they were fully dried and ready for use.
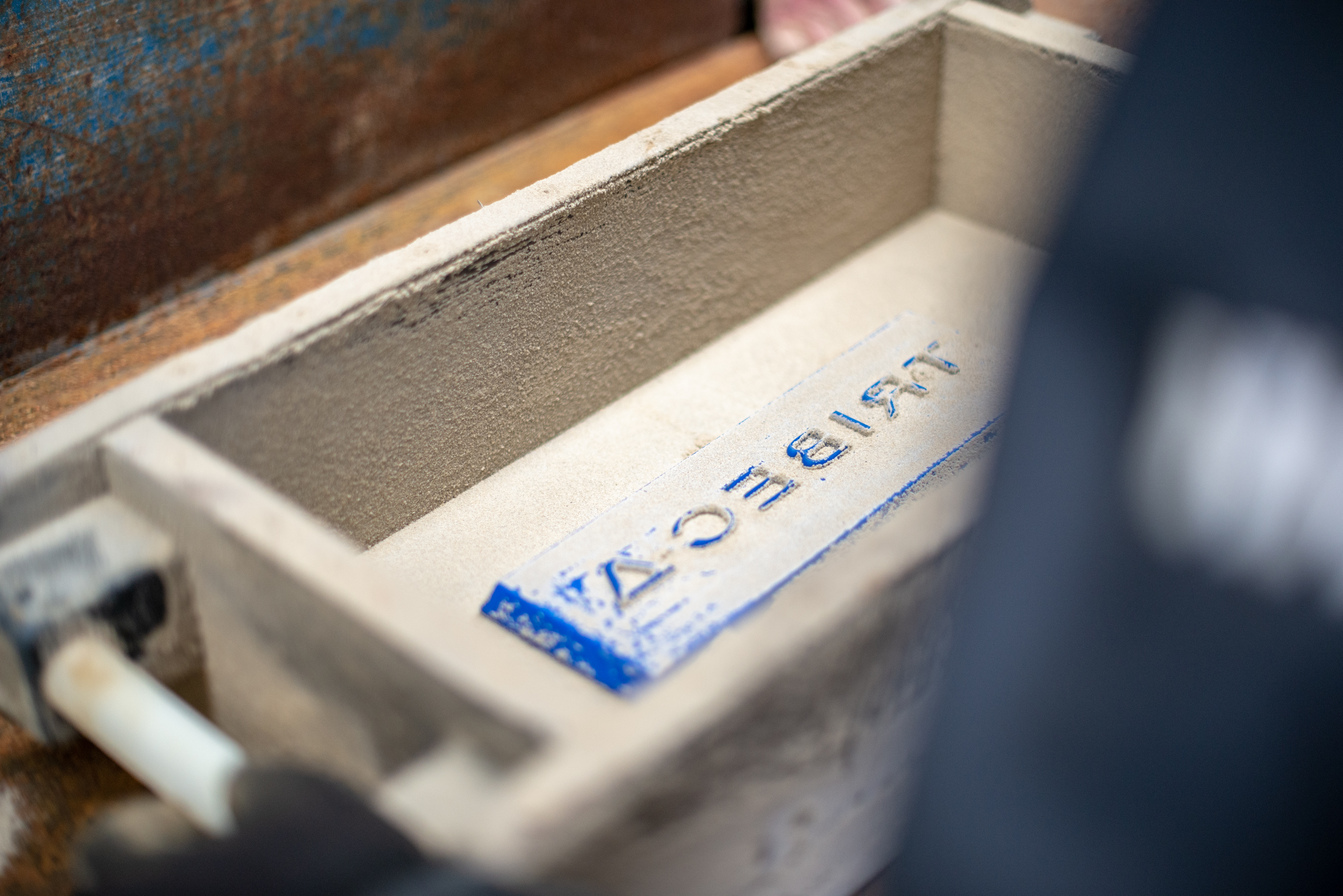
Shahpazov explains that tests showed the 50:50 clay-to-sand mix had a compressive strength of 6.5N/mm², the 75:25 mix measured 4N/mm², and the 100% subsoil brick reached 2.8N/mm². While the weakest option could have been used for the basement walls, the team opted for the strongest mix as a precaution.
The mortar was made from the same clay as the bricks. “We were lucky that the subcontractor had a bunch of Moldovan block layers who all came from a region where earth blocks were very common,” Shahpazov says. As a result, the team found the bricklaying process straightforward.
The earth bricks have proven highly successful, and Reef Group now plans to use them for the project’s second phase. The bricks have also passed a fire test—effectively firing them in the process—so they will now be incorporated into internal basement walls.
Shahpazov highlights additional potential applications for earth bricks, suggesting they could replace concrete floor screeds or be placed over CLT floor panels to add mass and reduce vibration. The clay could also be adapted for plaster or mixed with more straw for insulation purposes.
HG Matthews is currently testing earth brick panels for internal walls and assessing their compatibility with proprietary wind posts for added structural stability. Using earth bricks at Apex has already saved 10 tonnes of carbon—a figure expected to rise as they are used more extensively in later phases.
Perhaps most significantly, incorporating earth bricks into a commercial life sciences development like Tribeca sets a precedent, encouraging other developers to adopt them—ultimately contributing to a lower-carbon construction industry.